"
We have tried several times to introduce OKRs in the company and at the end the result was more like a todo list. Dmytro helped us to look at OKRs from alignment perspective, and we have started from articulating the company objectives which helped to bring everyone on board. Our teams enjoyed to work with Dmytro and discuss how to address different challenges, whether this is an improvement of the process or establishing new ways of working.
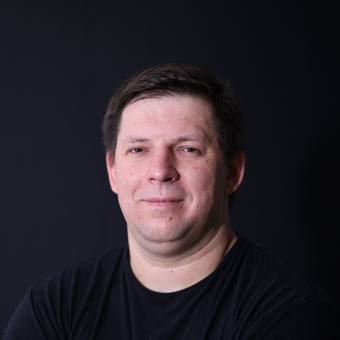
Project Duration: 3 months.
Request
A Danish deep-tech hardware company ATLANT 3D is a rapidly growing global pioneer that combines unique advanced technologies to enable smart atomically precise advanced manufacturing. The company carries an outstanding mission: building the future atomically precise advanced manufacturing technology and infrastructure for micro and nano-electronics, optics, and photonics on Earth and beyond.
The company turned to us with the challenge of building the foundation for the company's future culture and operating system. One of the key aspects that the company looked for was to align all teams toward ambitious company objectives and create a robust solution that would bridge strategy with tactics.
Process
The implementation process started with full engagement with the leadership team. Together with the CEO, we have refined the company's mission and outlined long-term objectives as 2 years company-wide OKR.
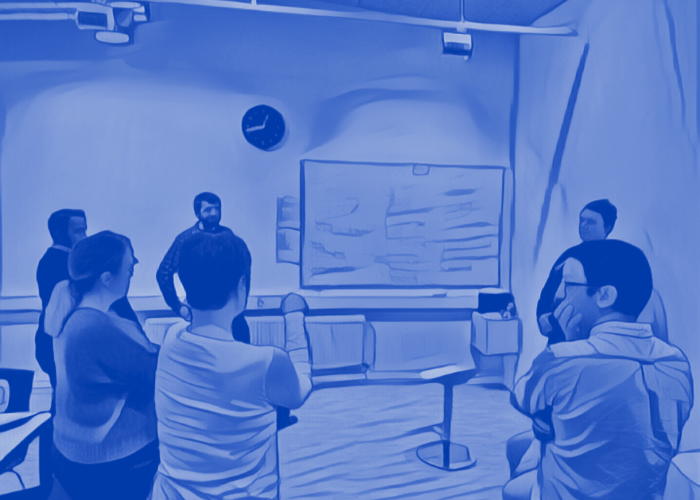
After communicating long-term company objective, we have trained the teams on OKR principles, after which they defined their OKRs for Q1 2023. While defining their OKRs, teams focused on alignment with the company's overall objectives and clarifying cross-team dependencies.
To secure the continuous evaluation of the teams' OKR progress, regular check-ins (weekly or bi-weekly) were introduced. Also, we have integrated OKRs into the company's project management tool: Monday.com
And to provide transparency, a dashboard has been created for a comprehensive view of the progress across all teams.
Going further, ATLANT 3D took the initiative to combine OKRs with KPIs, utilising KPIs for critical run activities and OKRs for changing activities.
Due to the company's nature, with hardware and supply chain lead times and long-term projects, not only did the teams define OKRs for the upcoming quarter but built a yearly OKR roadmap. Roadmaps provided a better direction and long-term overview not only for management but for teams as well.
The company also had a specific focus on standardizing the way hardware equipment was constructed, leading to a detailed description of critical processes. OKRs related to changes in these areas or processes were linked to these procedures, ensuring teams were mindful of which standard operating procedures needed adherence or adjustment.
Each quarter, the company holds an all-hands 2 days workshop, where they conduct a retrospective with the purpose of learning and improving, evaluate results for the previous OKRs, and update a rolling year OKR roadmap for each team.
Results
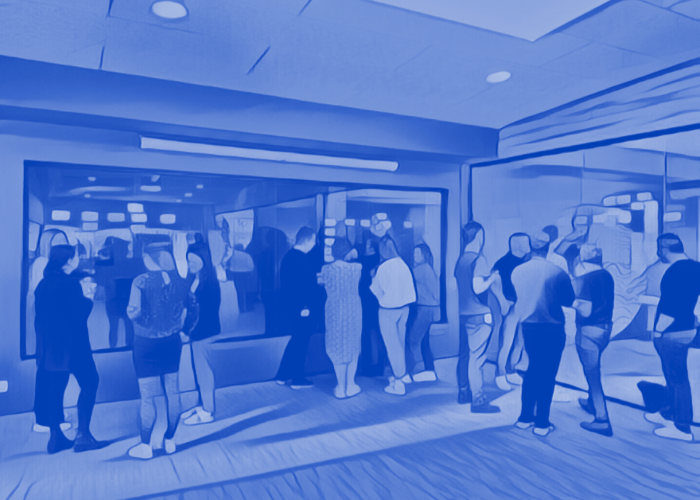
The OKR implementation at ATLANT 3D resulted in a company-wide alignment towards common goals, a more coherent guide for new employees, and a stronger cultural and operational foundation. It bridged the gap between strategic vision and practical tactics, fostering an environment of clear communication and alignment.
The integration of OKRs into the company's project management tool facilitated real-time progress tracking and ensured the entire team's focus was synchronously directed toward achieving the company's objectives. By incorporating KPIs and OKRs, ATLANT 3D successfully maintained a balanced focus on crucial ongoing activities and transformative ones.
Their unique approach to extending the OKR roadmap to a rolling year, considering the hardware and supply chain lead times, proved instrumental in planning and executing long-term projects. It brought foresight and long-term planning to teams, allowing them to anticipate challenges and act proactively.
The standardization and linking of critical processes to corresponding OKRs helped streamline procedures, promoting efficiency, and consistency. It led to a mindful approach to necessary adjustments in standard operating procedures, driving continuous improvement and innovation.